
3D print
I'm very passionate about the additive manufacturing and this was my interest for years. I build my own FDM printer in 2014 and started experimenting with the different designs and materials at home. I was always fascinated by the way how objects are created during the additive manufacturing process. Depositing filament in the FDM method or watching the emerging object from the resin bath on the SLA machines is so oddly satisfying I could watch it for hours.
01
Head Bands for Face Shield

I received an email from one of the companies I used to work with, about the project they are coordinated to help to battle a shortage of the PPE at the beginning of the COVID-19 pandemic.
Within 24 hours I tested several designs available online, prepared and optimised program for the Ultimaker printer.
I proposed to the general manager that we can use our company 3d printers and support this initiative.
On the same day we had six Ultimaker 2 printers, making headbands. They were running 24/7 for several weeks without a single fail during the print!
02
Part cleaning station
I designed this part cleaning station during setting up an Inspection Room. When the supplier quoted me £1500 for making part cleaning station. I decided it's time to design and make one. It cost us £180 in parts plus 3 hours of my time and 3 hours of maintenance engineer to assemble it. The device has been in use for 3 years now.
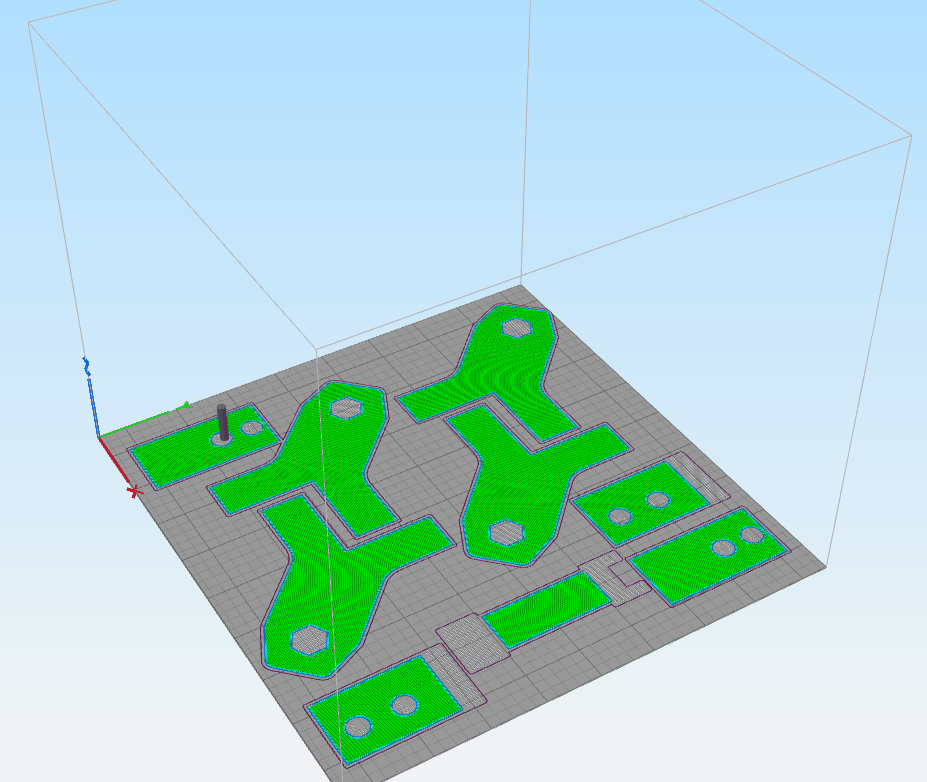

03
Consumable tooling

This is an example of how the traditional tooling can be replaced by the 3d printed one.
These loading jaws were used on one of out processes during part transfer into rolling chuck.
Traditionally made out of the H13 steel it costed £196 to purchase one set. Jaws were made out of the hard material which make difficult to set up the machine, due to the component damage caused during the loading.
Even the tool life wasn't a concern here the impact on the product quality and the setup time was.
After replacing steel jaws with the 3d printed substitutes made using a Colorfabb XT filament number of quality rejections drastically dropped in this process.
At the same time, setup time was also reduced as operators didn't have to spend hours optimising settings and polishing loading jaws.
04
HMI screen cover
One one of our machines we had a regular instances of the HMI screen cover failures.
Normally the whole unit was replaced due to the HSE regulations despite the fact the electronics inside was still fine. The fact that the unit was obsolete didn't help as it was impossible to obtain the spares.
In a couple hours I reverse engineered original cover and optimised design for the 3 d printing. I prototyped the first enclosure and applied further design changes. Final version of the cover was printed using reinforced flame-retardant filament. The new cover cost approx. £20 to 3d print compared to £1200 for sourcing complete unit replacement.
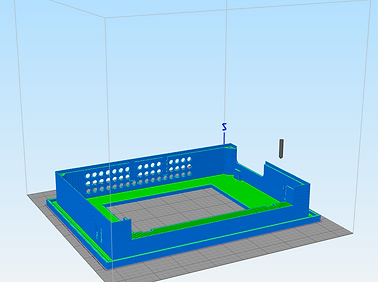